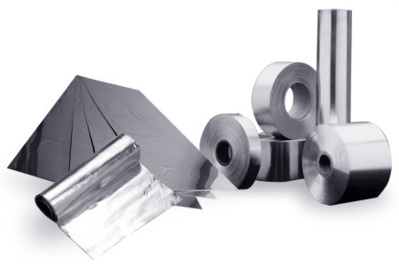
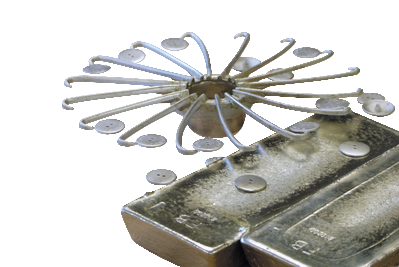
Centrifugal Casting
The METACONCEPT Group, specialising in the manufacture of tin-based alloys for the production of parts via centrifugal casting processes, has joined forces with NICEM (Italy), the leading European manufacturer of centrifugal casting equipment and elastomers.
This collaboration means that we can offer a range of unique services to our clients:
- Offering the best alloys on the market;
- Distributing a range of very high quality elastomers;
- Supplying all equipment and accessories necessary for designing and creating moulds.
The METACONCEPT Group also has a technical laboratory (with a full centrifugal line) where it offers training in the creation of silicone moulds.
This sheet covers equipment used with centrifugal casting materials.
Our centrifugal lines are designed for the fusion of metal elements (zamak, tin alloys) or polyester resin, with small and medium dimensions, in small and medium quantities.
The benefits of this technology, compared to traditional fusion systems (clay casting, die-casting, micro-fusion, lost wax casting, mechanical casting or gravity casting) are the speed and ease with which the fusion dies (moulds) can be made as well as the extremely straightforward fusion process.
This production technique does not require specialist staff.
With our very diverse range of equipment (dimensions, quantities), we meet the needs of markets such as:
- Fashion jewellery;
- Fashion accessories and leather goods;
- Furniture accessories (door knobs, handles, etc.);
- Metal or resin figurines;
- Eyewear;
- Dental prosthesis;
- Fishing weights;
- Various other industries.
A centrifugal line consists of a vulcaniser, a fusion furnace and a centrifuge. Its size is determined by the dimensions of the parts being created and the quantity of parts being produced.
Vulcaniser
|
Characteristics
|
Centrifuge
|
Characteristics
|
Fusion furnace
|
Characteristics
|
---|---|---|---|---|---|
P 300 PILO T
|
Semi-automatic vulcanising machine for the production of silicone and organic rubber (Ø 300 mm maxi) |
C 300 PILOT
|
Centrifuge with a station accepting moulds from 230 mm to 300 mm in Ø
|
F50 PILOT
|
Automatic electric furnace for the fusion of tin and zinc alloys (zamak) |
P 400/16’’
MATIC |
Automatic vulcanising machine for the production of silicone and organic rubber (Ø 400 mm maxi) |
C 400/16’’ MATIC
ou CSE 400SC |
Automatic electric centrifuges with a station accepting moulds from 230 mm to 400 mm in Ø
|
F80 MATIC F120 MATIC
|
Automatic electric furnaces for the fusion of tin and zinc alloys (zamak)
|
P 400/16’’
MATIC |
Automatic vulcanising machine for the production of silicone and organic rubber (Ø 400 mm maxi)
|
C 400 MATIC R
|
Centrifuge with a hot chamber and station (particularly useful for polyester resins) accepting moulds from 230 mm to 400 mm in Ø)
|
NO
|
NC
|
P 400/16’’
MATIC |
Automatic vulcanising machine for the production of silicone and organic rubber (Ø 400 mm maxi) |
TRSME 350/3
TRSME 400/3 |
Semi-automatic electronic centrifuge with 3 stations accepting moulds from 230 mm to 350 mm or 400 mm in Ø, depending on the model of the machine
|
F80 MATIC / F120 MATIC
|
Automatic electric furnaces for the fusion of tin and zinc alloys (zamak)
|
P 400/16’’
MATIC |
Automatic vulcanising machine for the production of silicone and organic rubber (Ø 400 mm maxi) |
TRSE 300/8 –
F220 ou TRSE 300/8 – F350 |
Automatic electronic centrifuge with 8 stations accepting moulds from 230 mm to 300 mm or 400 mm in Ø, depending on the model of the machine
|
F220 MATIC F350 MATIC
|
Integrated furnaces
|
P 500
MASTER |
Automatic vulcanising machine for the production of silicone and organic rubber (Ø 500 mm maxi) |
C 500 MASTER
|
Centrifuge with a station accepting Ø 500 mm moulds (do not use 230 mm moulds)
|
F120 MATIC F220 MATIC F350 MATIC
|
Automatic electric furnaces for the fusion of tin and zinc alloys (zamak)
|
P 700
MASTER |
Automatic vulcanising machine for the production of silicone and organic rubber (Ø 700 mm maxi) |
C 700/16’’
|
Automatic electronic centrifuge with a station accepting moulds from Ø 500 to 700 mm
|
F120 MATIC F220 MATIC F350 MATIC
|
Automatic electric furnaces for the fusion of tin and zinc alloys (zamak)
|
Complément d’appareils pour ligne de centrifugation
Designation
|
Characteristics
|
Use
|
---|---|---|
System – ASP MATIC 
|
Talc suction system
|
Used when closing the mould to remove surplus talc. Recommended and obligatory, in accordance with occupational health standards
|
ASP/2 MATIC vacuum
|
Activated carbon vacuum to purify the smoke
|
Used when opening the moulds to remove the parts
|
TRA – MATIC table 
|
  Forced air cooling table
|
Accelerated cooling of rubber dies. Used for moulds from 230 mm to 400 mm
|
Accessories
For silicone vulcanisation, you should use mould boxes from 230 mm to 700 mm, depending on the parts that you are wanting to create. The size of the ladle also depends on the type of parts that you are going to produce.
Have you defined the type of application? Contact us as our staff will be happy to assist you in deciding which equipment and materials to choose.
Application
|
Uses
|
Characteristics
|
---|---|---|
PILOT casting line
|
Economical, suitable for the production of small quantities, dimensions and sizes
|
For application in the areas of dental prosthesis, figurine manufacture, eyewear, etc.
|
400 series casting line
|
Economical, suitable for the production of small and medium quantities and dimensions
|
80% of casting lines are equipped with a 400 series either in a manual or semi- automatic line
|
500 series casting line
|
Suitable for the production of small and medium quantities, for medium or large parts
|
Used in areas such as furniture, leather accessories and manufacturing, decoration, various electrical and mechanical applications.
|
700 series casting line
|
Suitable for the production of small and medium quantities, for medium or large parts
|
Used in areas such as furniture, leather accessories and manufacturing, decoration, various electrical and mechanical applications.
|
The semi-automatic TRSME and automatic TRSE centrifuges have been specially designed for high volume productions (series greater than 20,000 pieces). They can be used for applications such as costume jewellery, key rings and in the engineering industry.
The product safety datasheet below is available upon request to the METACONCEPT Group.
The implementation process is specific to the chosen medium (metal or polyester resin) and the characteristics of the part being produced, The METACONCEPT Group’s technical department will advise you on which silicone to choose and the appropriate implementation procedure.
To prevent burns caused by the molten metal, it is advisable to wear a protective apron, shoes, gloves, helmet and glasses.
Do not smoke at the workstation.
The workstation must be well ventilated.
Wash your hands when leaving the workstation.
Comments:
All of the information contained in this document is provided for informational purposes only and the METACONCEPT Group will not be held liable for it.