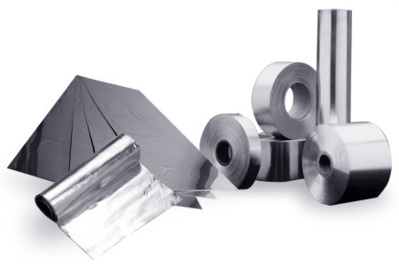
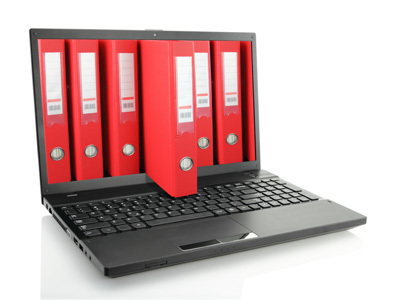
Technical Handbook
The technical data sheets created by the METACONCEPT Group are dedicated to tin-based alloys as well as hard brazing. Tin-based alloys are generally used to assemble metal parts at a temperature below 450°C. This brazing procedure is called“soft soldering”.
For all types of soldering it is necessary to use a flux (internal or external) which removes the layer of oxides and at the same time protects the parts and the solder from oxidation during the soldering process.
These alloys can be used for applications other than soft soldering, such as:
- Costume jewellery
- Pipe bending
- Safety (thermal fusibles)
- Babbitt alloys
Brazing is an assembly method which is carried out between 600° and 850°C. It requires the use of a flux (internal or external) which removes the oxide layer whilst protecting the parts and the solder from oxidation during the brazing process (except copper/phosphorous solders which self-flux on the copper).
Soft soldering and other brazing methods
Techniques
|
Filler metal
|
Melting T°
|
Heating tools
|
Metals being assembled
|
Implementation
|
Solidity
|
---|---|---|---|---|---|---|
Soft soldering | Tin-based alloy |
140° – 450°
|
– Soldering iron – Blow torch – Solder bath – Wave – Induction – Hot air |
Almost all |
Easy
|
Average
|
Brazing | Alloys made from: – Copper – Silver – Zinc – Phosphorous |
600° – 850°
|
Dual gas torch | All except : – Zinc – Lead – Tin |
Good
|
Good
|
Brass welding | Brass (copper and zinc) |
850° – 950°
|
Dual gas torch | – Steel – Stainless steel – Cast iron – Copper |
Average
|
Good
|
Welding | The same type of parts being assembled |
1500° – 2000°
|
Electrival station | All metals able to withstand high temperatures |
Difficult
|
Good
|
Implementation
Main metals used for the implementation of alloys in soft soldering and brazing
Description
|
Symbol
|
Density
g/cm3 |
Melting
point |
Properties
|
Uses
|
---|---|---|---|---|---|
Antimony
|
Sb
|
6,68
|
630,5°
|
– ncreases the melting temperature
of the alloy – Strengthens it – Slightly improves its wettability – Slightly breakable metal |
The metal’s use in batteries and Babbitt alloys represents half of its overall consumption.
|
Silver
|
Ag
|
10,5
|
962°
|
– Strengthens the alloy.
– Improves the “wettability” – Used in small quantities in the manufacture of tin-based alloys. |
Tin/silver alloys are primarily used in electronics and in the automotive sector. Silver-based alloys, for Cu/P-based brazing, are specifically used in plumbing; silver- based brazing is used for all types of work where the mechanical strength needs to be increased.
|
Bi
|
9,78
|
271,3°
|
– Very breakable metal
– As with antimony and gallium, bismuth increases in volume during solidification. |
Often used for its fusibility and controllable dimensional change properties.
|
|
Copper
|
Cu
|
6,68
|
1084°
|
– Strengthens the alloy.
– Prevents “leeching” (dissolution of the parts’ copper into the solder bath). – Ductile metal with particularly high electrical and thermal conductivity. – Very resistant to corrosion |
It is used in areas such as:
– Electrics – Electronics – Microprocessors – Heat exchangers – Building – Pipes for soft soldering and brazing |
Tin
|
Sn
|
7,30
|
231,9°
|
– Malleable metal, fairly
ductile. – Resistant to corrosion from salt and fresh water, but may be attacked by strong acids. |
Used in practically all sectors where soft soldering is recommended.
|
Indium
|
In
|
7,31
|
156°
|
– Malleable metal, resistant to
corrosion. – Soft metal like lead. – Reduces the temperature of the alloy |
Widely used in flat screens. It is used in:
– Avionics – The nuclear industry – Mechanics (bearings and rollers) – medecine – Glass coatings |
Phosphorous
|
P
|
2,40
|
NC
|
The higher the percentage of phosphorous in the Cu/P compound, the greater the fluidity of the alloy but also the more its mechanical characteristics are reduced.
|
Phosphorous-based brazing alloys are used in the cooling and air-conditioning sector and for any application where the assemblies must resist stresses resulting from expansion, shrinkage or vibrations.
|
Lead
|
Pb
|
11,35
|
327°
|
– Non-breakable
– Good value for money – Soft metal – Oxidises over time |
Prohibitions of the use of lead in various applications are increasing because of its toxicity. Still commonly used in plumbing, roofing and zinc works.
|
Zinc
|
Zn
|
7,15
|
419°
|
Excellent joint stability (does not move over time) and solidity.
|
Rarely used in soft soldering. It is mainly used in the composition of brazing alloys.
|
Mechanical assembly: | An assembly enabling two or more parts to be fixed together with a view to automating their operation. |
Electrical assembly: | An assembling combining and optimising the conduction between several parts with different properties. |
Soldering: | An action consisting of soldering with an alloy whose melting temperature is lower than that of the surfaces being soldered. |
Brazing: | An assembly operation carried out between 600 and 800°C. |
Soft soldering: | Generally tin based, it refers to assemblies created at temperatures generally lower than 450°C. |
Bending: | An operation consisting of adding a curve to a hollow or tubular part by injecting it with a fusible alloy which will be removed by raising the temperature. |
Casting: | An operation consisting of pouring the metal into the mould. |
Degrees Celsius (°C): | = °F – 32 (x 5 : 9) |
Degrees Fahrenheit (°F): | = °C (x 9 : 5) + 32 |
Electroplating: | An operation, also known as surface treating, consisting of applying a thin layer of protective metal or alloy to a part using electrolysis. |
Electroforming: | The manufacture or reproduction of imprints produced by the electrolytic deposition of a metal on a mandrel and separated by demoulding. |
Tinning: | A technique consisting of applying a very thin layer of tin to a metal part. |
Eutectic: | The specific property of an alloy that goes from a solid state to a liquid state without passing through the mushy phase. This melting point of the eutectic alloy varies in accordance with the properties of the components. |
Forming: | An operation consisting of forming a part, in other words giving it a shaped, convex or concave appearance or creating an embossed design. |
Laminating: | An operation consisting of compressing the metal to turn it into sheets, strips, etc. |
Moulding: | An operation consisting of producing a part from a mould template. |
Recycling: | An operation consisting of collecting metallic scraps or residues from an alloy or a metal to give them a second life by refining them and removing impurities. |
Slabbing: | An operation consisting of stamping, cold forming or deforming a part outwards to create an embossed design. |
Welding: | An action consisting of permanently welding two parts together using an alloy whose melting temperature is the same as that of the parts being assembled. |
Surfacing: | An operation consisting of polishing the surface of a raw part. |
Nothing to report
To prevent burns caused by the molten metal, it is advisable to wear a protective apron, shoes, gloves, helmet and glasses.
Do not smoke at the workstation.
The workstation must be well ventilated.
Wash your hands when leaving the workstation.
Comments:
Always use a flux suited to the intended use. Contact our technical department to ascertain which product is most suited to your application.
All of the information contained in this document is provided for informational purposes only and the METACONCEPT Group will not be held liable for it.