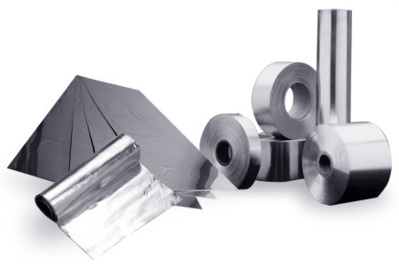
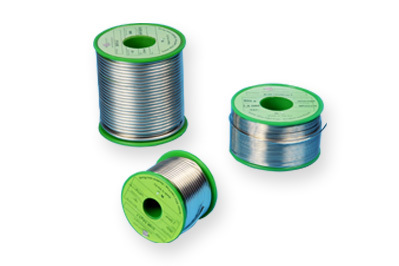
Solid And Cored Wires
Four characteristics used to describe wire are the alloy, the diameter, the type of flux and the winding.
The chosen flux can be integrated into the wire or left separate, depending on the manufacturing process and the end use. There are in fact thousands of possibilities from which METACONCEPT has selected an extensive range of consistent products suitable for all major types of applications. Waste originating from the use of these products can be recycled.
Contact our recycling department to find out more.
Alloys available for cored wires
This table shows the most commonly used alloys in the area of soft-soldering:
EN 29453 classification
|
Density g/cm3
|
Solidus / Liquidus
|
Comments
|
---|---|---|---|
Sn40 – Pb60
|
9,72
|
183°C – 235°C
|
All applications
|
Sn50 – Pb50
|
9,32
|
183°C – 215°C
|
Sheet metal works
|
Sn60 – Pb40
|
8,91
|
183°C – 190°C
|
Electrics. electromechanics
|
Sn62 – Pb36 – Ag2
|
8,81
|
178°C- 190°C
|
All applications
|
Sn63 – Pb37
|
8,79
|
183°C Eutectic
|
Electronics
|
Sn96 – Ag4*
|
7,39
|
221°C Eutectic
|
Lead-free* – All applications
|
SAC 305*
|
7,3
|
217°C – 219°C
|
Lead-free* – Electronics
|
SAC 307*
|
7,3
|
217°C- 228°C
|
Electronics
|
Sn97 – Cu3*
|
7,33
|
227°C- 310°C
|
Lead-free* – All applications
|
Sn99 – Cu1*
|
7,3
|
227°C Eutectic
|
Lead-free* – Electrics, electronics
|
(*) Lead-free alloys – European standard no. 2000 / 53 / CE
Integrated fluxes
Type
|
Nature
|
JSTD004 Classification
|
Level of acidity (mg KOH/g)
|
Halogen rate (wt %)
|
Residue removal
|
---|---|---|---|---|---|
MRS1
|
Inorganic
|
FSW21
|
NC
|
10
|
Clean with water
|
MRS2
|
Resin
|
ROM1
|
175
|
1,3
|
Clean with a solvent
|
MRS7
|
Resin
|
ROM1
|
220
|
1
|
Clean with a solvent
|
MSP7
|
Organic
|
ROM1
|
130
|
1,1
|
Clean with a solvent
|
MSP15
|
Organic
|
ROLO
|
386
|
0
|
Clean with a solvent
|
MSPALU
|
Inorganic
|
INH1
|
NA
|
NA
|
Clean with water
|
MZP3
|
Inorganic
|
INH1
|
NA
|
6,5
|
Clean with water
|
Have you defined the type of application? Contact us. Our technical staff will be happy to assist you in choosing the diameter, the type of flux and the alloy.
Alloys available for solid wires
EN 29453 Classification
|
Density
|
Solidus / Liquidus
|
Comments
|
---|---|---|---|
Pb99,5 – Sb0,5
|
11,33
|
322°C – 325°C
|
Bulb manufacture
|
Sn5 – Ag2 – Pb93
|
11,13
|
296°C – 301°C
|
Tinning and cracking enamelled copper wire
|
Sn30 – Pb70
|
10,13
|
183°C – 255°C
|
Copper, zinc and steel brazing
|
Sn40 – Pb60
|
9,72
|
183°C – 235°C
|
Copper, zinc and steel brazing
|
Sn40 – Pb55 – Zn5 (Otaline)
|
9,51
|
170°C – 179°C
|
For aluminium brazing
|
Sn43 – Pb43 – Bi14
|
9,2
|
144°C – 163°C
|
Jewellery, tinware, models
|
Sn50 – Pb50
|
9,32
|
183°C – 215°C
|
Zinc elements
|
Sn60 – Pb40
|
8,91
|
183°C – 190°C
|
Copper, zinc, steel and nickel brazing
|
Sn62 – Pb36 – Ag2
|
8,81
|
178°C
|
Mainly copper brazing
|
Sn63 – Pb37
|
8,79
|
178°C – 190°C
|
Eutectic, mainly copper brazing
|
Sn70 – Zn30
|
7,24
|
199°C – 320°C
|
Heat sprays (metal spraying) – All applications
|
Sn96 – Ag4
|
7,39
|
221°C
|
Eutectic – lead-free* – All applications
|
SAC 305
|
7,3
|
217°C – 220°C
|
Electronics – Lead-free*
|
SAC 307
|
7,3
|
217°C – 228°C
|
All applications – Lead-free*
|
Sn97 – Cu3
|
7,33
|
227°C – 310°C
|
Electrics, electronics – Eutectic – Lead-free*
|
Sn99 – Cu1
|
7,3
|
227°C
|
Eutectic – lead-free* – All applications
|
Sn100
|
7,28
|
232°C
|
Eutectic – lead-free* – All applications
|
(*) Lead-free alloys – European standard no. 2000 / 53 / CE
Standard diameters and spools
With standard dies it is possible to create wires with a minimum diameter of 0.3 mm and maximum diameter of 6 mm. The main intermediary values are: 0.5, 0.7, 1.0, 1.5, 2.0, 2.5, 3.0, 4.0 and 5.0 mm. Weight of commonly used spools: 100 g, 250 g, 500 g, 1 kg, 2.5 kg, 5 kg and 20 kg. For high volume industrial applications, 25 kg, 30 kg and 100 kg containers are also available.
Types of spools and packaging
The type of spool used varies depending on the desired volume. For standard uses, AMPRA spools are preferred. However, for intensive industrial uses, DIN spools are recommended. The following tables list the spools and their dimensions depending on the net weight of the packaged wire, as well as the standard packaging.
Weight
|
Type
|
Packaging
|
Type
|
Packaging
|
---|---|---|---|---|
100 g
|
AMPRA
|
 10 kg box
|
DIN 26/2
|
 8 kg box
|
250 g
|
AMPRA
|
 6 kg box
|
DIN 50
|
 5 kg box
|
500 g
|
AMPRA
|
 12 kg box
|
DIN 63
|
 10 kg box
|
1 kg
|
AMPRA
|
 12 kg box
|
DIN 80
|
 16 kg box
|
2.5 kg – 3 kg
|
AMPRA
|
 15 kg box
|
DIN 63
|
 10 kg box
or 2.5 kg spools 12 kg box or 3 kg spools 16 kg box or 4 kg spools |
5 kg
|
AMPRA
|
15 kg box
|
DIN 80
|
20 kg box
|
20 kg
|
NC
|
NC
|
DIN 180
|
20 kg box
|
25 kg
|
Drum
|
NC
|
NC
|
NC
|
30 kg
|
Drum
|
NC
|
NC
|
NC
|
100 kg
|
Drum
|
NC
|
NC
|
NC
|
Details of AMPRA spools
AMPRA type
|
A (mm)
|
B (mm)
|
C (mm)
|
D (mm)
|
---|---|---|---|---|
100 g
|
18
|
14
|
50
|
14
|
250 g
|
39
|
34
|
50
|
14
|
500 g
|
37
|
32
|
66
|
23,5
|
1 kg
|
68
|
63
|
66
|
23,5
|
3 kg
|
93
|
87
|
94
|
29
|
5 kg
|
104
|
99
|
120
|
46
|
Details of DIN spools
DIN type
|
D1
|
D2
|
D3
|
D4
|
L1
|
L2
|
---|---|---|---|---|---|---|
100 g
|
39
|
21
|
9
|
N/A
|
44
|
38
|
250 g
|
50
|
32
|
11
|
15
|
50
|
38
|
500 g
|
63
|
40
|
11
|
15
|
63
|
49
|
1 kg
|
80
|
50
|
16
|
24
|
80
|
64
|
2 kg
|
100
|
63
|
16
|
24
|
100
|
80
|
5 kg
|
125
|
80
|
16
|
24
|
125
|
100
|
20 kg
|
300
|
180
|
51.5
|
N/A
|
103
|
85
|
25 kg and 30 kg drums > 360 mm high – 310 mm in diameter
- Electricity
- Plumbing – Sanitary facilities – Heating
- Electromechanics
- Electronics
- Tinware
The product safety datasheet below is available upon request to the METACONCEPT Group.
In the case of a solid wire (non-fluxed), the parts must be clean, degreased and deoxidised. First, apply the appropriate flux to the parts.
Heat the parts using a propane or acetylene torch, or a soldering iron.
The parts must be heated to around 20°C above the liquidus temperature.
Melt the filler metal onto the parts being assembled to form a regular bead.
Allow the parts to cool without moving them. When the parts have returned to room temperature, brush the soldering beads using a metallic brush. If necessary, clean the assembly with clean water or water with a touch of citric or formic acid (1 to 2 %) in the case of water-soluble residues.
Use a solvent for residues from rosin or resinous fluxes.
In the case of a flux-cored wire (integrated flux), the fluxing stage described above is not always necessary. These wires may also be used with an automatic soldering machine. In this case, the diameter of the wire must be perfectly adapted to the diameter of the nozzle. In addition, it is advisable to use a wire where the % of flux is greater than that used for manual soldering.
Precaution for use
Do not smoke at the workstation.
The workstation must be well ventilated.
Wash your hands when leaving the workstation.Comments:
Always use a flux suited to the intended use. Contact our technical department to ascertain which product is most suited to your application.All of the information contained in this document is provided for informational purposes only and the METACONCEPT Group will not be held liable for it.